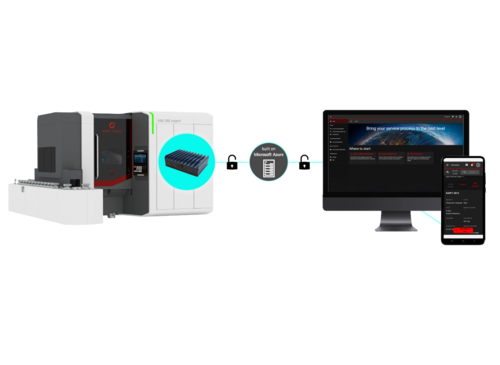
Digital solutions from KAPP NILES are displayed in the software platform KN assist. Our digital products aim to generate the greatest possible added value for you.
Quality, availability, efficiency, resources, user-friendliness and service play a major role here. We focus on the core areas of connectivity, production and support in order to master all current and future challenges together with you.
The digital solutions thus stand for a perfect interaction of efficient processes around our machines.
Process Monitoring can be defined as component-specific monitoring and evaluation of the grinding and dressing process. It is possible to generate an action instruction from the sensor signals. Various characteristic values are formed from time signals, in the simplest case these can be maximum or RMS (Root-Mean-Square) values of the signals. The characteristic values are then combined with the known project data via algorithms and processed into indices, such as a noise or damage of grinding worm index. Process Monitoring has interfaces to further functionalities (such as part tracing) and an export function for off-machine analysis.
Transmissions in e-mobility do not only have to be efficient, but also quiet. Up to now, workpieces with negative noise behaviour have usually been detected in EOL or in some cases on the roller test bench. The common random measurement of machined workpieces can only detect individual deviations, which later have an effect on the noise behaviour of the gearbox. This is where the Process Monitoring developed by KAPP NILES comes into the picture.
Based on internal machine control signals and signals from specifically used acceleration sensors, characteristic values are formed to assess the grinding process.
This makes it possible to identify workpieces with noticeable noise during machining effectively and cost-effectively. This reduces the amount of scrapped parts.
In addition to noise anomalies, other deviations can also be detected with the support of Process Monitoring in order to meet the high quality requirements in the field of e-mobility.
The data obtained with Process Monitoring can be used, among other things, to establish a correlation between the processing machine and the transmission test bench or measuring machine. This makes it possible to derive further findings for process optimisation.
Condition Monitoring from KAPP NILES makes it possible to monitor the condition of linear and rotary axes with regard to wear. The wear is determined by reference runs after workpiece machining and can be started manually or via a timer function. No retooling is necessary for this; the reference run is carried out independently of the tooling being set up. The condition is evaluated by means of indices, after which a prognosis is made about the durability of the axes. Once the wear condition has been transmitted as an index per axis, a visualisation of the wear progression takes place via the HMI. Condition Monitoring has interfaces to further functionalities (such as part tracing).
Digital Service - Remote Service
Highlights
- Faster and simpler support and solution finding through targeted communication via a ticket system (no e-mail traffic)
- Documentation, operating instructions and e-plans for each machine available digitally and up-to-date
- Transparent communication about the status of the service request
With the Remote Service, KAPP NILES provides its customers with a self-developed solution to ensure fast and efficient support in service cases. The use of modern communication technologies enables a targeted and effective solution finding.
KAPP NILES‘ Remote Service offers a wide range of functions to ensure the smooth processing of service requests. Customers can submit their requests in a structured and efficient manner via a ticket system. Support is provided through various communication channels such as live video, voice over IP, chat and whiteboard functions. This allows problems to be identified quickly and solutions to be communicated directly.
Another advantage is the comprehensive documentation of service activities. Detailed documentation is created for each machine and stored in the system archive. This documentation enables quick access to the service history and ensures transparency and traceability.
The status of the service request and the documentation can be called up in real time to create transparency.